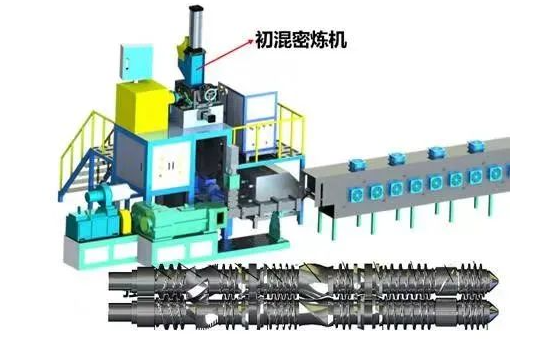
圖:“密煉機+連續(xù)混煉機”裝備
我國是世界第一大輪胎生產與消費國,2023年輪胎產量約占全球56%,已成為中國制造的重要標志。近年來,歐美等發(fā)達國家通過輪胎標簽法、輪胎“雙反”調查以及技術壁壘等手段來制約中國橡膠輪胎行業(yè)的高質量發(fā)展。
基于此,青島科技大學聯(lián)合益陽橡膠塑料機械集團有限公司、中策橡膠集團股份有限公司、青島雙星輪胎工業(yè)有限公司、浦林成山(山東)輪胎有限公司和特拓(青島)輪胎技術有限公司等單位組建研究團隊,成功研發(fā)出高性能子午線輪胎生產體系的關鍵技術裝備與產業(yè)化,并在30余家企業(yè)中獲得產業(yè)化應用,相關產品銷往歐美等100多個國家和地區(qū),為中國輪胎由“中國制造”邁向“中國創(chuàng)造”奠定了技術基礎。該技術于日前獲得2024年度中國石油和化學工業(yè)聯(lián)合會科技進步一等獎。
據該成果第一完成人青島科技大學汪傳生教授介紹,如今全球橡膠輪胎行業(yè)競爭,技術創(chuàng)新是關鍵。為此,研究團隊緊緊圍繞橡膠輪胎行業(yè)高質量發(fā)展的痛點難點問題開展技術攻關,實現了技術裝備、輪胎設計和工藝技術三方面的重大創(chuàng)新。
一是技術裝備創(chuàng)新,發(fā)明出子午線輪胎膠料高質高效連續(xù)混煉方法與成套裝備。
輪胎膠料的混煉過程中,填料的均勻分散和橡膠基質分子鏈的適宜長度是決定輪胎性能的關鍵因素。橡膠材料對剪切的高度敏感性增加了混煉過程的復雜度。在混煉時,橡膠容易迅速升溫,進而導致在高溫條件下發(fā)生分子鏈氧化斷鏈,這對保持材料性能穩(wěn)定性構成了巨大挑戰(zhàn)。此外,剪切變稀現象導致膠料黏度下降,使得納米級填料聚集體難以有效破碎和均勻分散,從而影響最終產品的質量和性能。傳統(tǒng)的“密煉—停放—密煉”多段混煉模式,雖解決了溫度控制問題,卻導致生產效率大幅降低,多次加熱和冷卻產生的無效熱歷程極大浪費了能源,混煉過程能耗占據了輪胎制造總能耗的55%左右。這不僅反映了橡膠混煉技術的復雜性和加工難度,也凸顯了行業(yè)迫切需要技術創(chuàng)新,以實現高效、低碳、可持續(xù)發(fā)展。
面對這一挑戰(zhàn),研究團隊攻堅克難,在國際上首次提出了串聯(lián)式連續(xù)混煉新概念和恒溫強剪切反應混煉新機制,發(fā)明了“空間適時遷移”的模塊化組合式混煉方法與技術,研制了功能性轉子的系列串聯(lián)式連續(xù)混煉成套裝備,攻克了混煉恒溫調控與剪切速率協(xié)調平衡難題。與傳統(tǒng)混煉技術相比,新技術產能提升40%以上,能耗降低25%以上,分散度提高2至3級,綜合性能提高15%~20%。依托該技術,在益陽橡機建成國內首個密煉機數字化制造基地,成為我國橡膠機械行業(yè)數字化制造標桿。
二是輪胎設計創(chuàng)新,研發(fā)出高性能子午線輪胎趾口和胎肩耐脫層系列新結構。
輪胎是多種材料復合而成的柔性殼體。在輪胎退賠的所有質量問題中,占比80%以上的趾口和胎肩脫層問題嚴重影響輪胎使用壽命和行車安全,成為子午線輪胎的一大頑疾。
面對這一難題,研究團隊迎難而上,厘清了輪胎脫層問題主要源于輪胎幾何結構、物理非連續(xù)及使用過程應力、疲勞、熱、氧的綜合循環(huán)作用。由此,研究團隊首次提出并建立了“輪胎疲勞失效熱力耦合”模型,并結合自主研發(fā)的熱力學仿真軟件,創(chuàng)新結構優(yōu)化設計方法,發(fā)明了系列新結構,解決趾口和胎肩應力集中與熱聚集難題,在國際上形成中國輪胎抗載安全的特色和優(yōu)勢。與國際輪胎巨頭相比,采用該結構的輪胎耐久性提高20%以上,胎圈耐久性提高3倍以上,產品性能國際領先。
三是工藝技術創(chuàng)新,開發(fā)出高性能子午線輪胎生產體系成套工藝技術軟件包。
輪胎制造加工工藝也是影響輪胎質量的重要因素?;鞜捘z質量批次不穩(wěn)定、膠料半成品中的氣孔、雜質、凝膠等微缺陷是誘發(fā)輪胎脫層、降低輪胎耐久性和抗載性的根本原因。而現有的輪胎制造工藝技術難以滿足高性能子午線輪胎的質量穩(wěn)定性、智能化生產和數字化管理等一系列需求。
基于這些需求,研究團隊凝心聚力,成功構建了輪胎全生命周期數字化設計管理平臺,開發(fā)了智能制造成套工藝包,形成了智能設計、智能控制、智能生產的輪胎制造全產業(yè)鏈技術路線與工藝流程,建成了綠色輪胎智能制造試點示范線,并實現產業(yè)化。